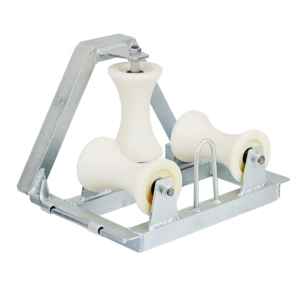
Introduction to Cable Round Roller Production
When you embark on understanding the production of cable round rollers, you’re peering into a critical process within the cable manufacturing industry. The rollers you’ll encounter are pivotal in shaping and compacting cable cores, ensuring they meet required specifications for electrical conductivity and strength.
Materials: Typically, rollers are crafted from robust materials such as steel for durability, given the repetitive mechanical processes they undergo. It’s also worth noting that the copper or aluminum wires that the rollers handle are chosen based on properties like high electrical conductivity and malleability.
- Manufacturing Process: The intricacies of production involve a series of complex steps, starting from designing the rollers to the final machining. The rollers’ profiles are meticulously engineered to compact the cable’s conductor.
- Benefits: The use of rollers in the production process isn’t just for shaping; it’s a method to reduce material consumption and improve the overall electrical attributes of the cable. By tightly compacting the strands of copper or aluminum, less insulation is needed, which streamlines both material use and costs.
Remember, each component produced follows the strictest industry standards to ensure reliability and efficiency in the cables you use daily. As you delve deeper into this field, appreciate the precision engineering that ensures the cables that power your home or office are of the highest quality.
Materials and Components
In cable round roller production, the quality of your final product heavily relies on the choice of materials for both conductors and insulating layers. You’ll encounter a range of materials with differing electrical and mechanical properties suited for various cable types.
Conductor Materials
Your cable’s performance is primarily influenced by its conductor, which is most commonly made of copper or aluminum. Copper is favored for its superior conductivity and durability, but aluminum is often chosen for its cost-effectiveness and lighter weight.
- Copper: Offers high conductivity and is less susceptible to corrosion.
- Aluminum: Provides a lighter alternative with good conductivity at a lower material cost.
Insulation and Sheathing
Insulation and sheathing materials protect the integrity of your cable’s conductor and ensure safe operation. Polyethylene, due to its strong insulating properties and resilience to environmental factors, is a typical choice for both insulation and outer sheathing.
- Polyethylene: A thermoplastic material that’s flexible and resistant to moisture.
- Crosslinked Polyethylene (XLPE): Used for its enhanced thermal and chemical properties, especially in high voltage applications.
Design and Engineering
When you’re looking to create a cable, the design and engineering phase is vital. This stage will determine the cable’s performance regarding its roundness, strength, and flexibility. Precision in calculations and component selection is the foundation for high-quality cable production.
Calculating Cable Specifications
To ensure the desired properties such as high strength and adequate elasticity, you’ll first need to calculate the cable specifications. Stranding is a crucial factor in this, impacting the cable’s final thickness and roundness. Here’s a simple guide to begin with:
- Roundness: Measure the cross-sectional height of the material. For round wires, this is the wire diameter.
- Strength: Determine the yield point of the material, which is its ability to withstand loads without permanent deformation.
- Elasticity: Assess the modulus of elasticity (E) to understand how the cable will resume its shape after force is applied.
Using these measurements, use the following equations to determine the minimal and maximal guide roller diameters:
- Minimal Diameter (Dmin) = (function of material height, yield point, modulus of elasticity)
- Maximal Diameter (Dmax) = (dependent on material and process requirements)
Selection of Cable Components
Selecting the right components for your cable involves a detailed understanding of the intended application. The key considerations include:
- Material: Choose materials that offer the needed balance between flexibility and strength.
- Guide Rollers: Opt for rollers that align with your calculated specifications to ensure proper compaction and stranding. Profiled rollers may be beneficial for specific applications.
- Stranding Machine Settings: Adjust the stranding machine to work at optimal speeds without compromising the compaction process.
A table for roller selection based on material properties could look like this:
Material Type | Roller Diameter | Roller Profile | Notes |
High-strength Alloy | X mm – Y mm | Standard/Profiled | Suitable for high-speed stranding |
Standard Copper | X mm – Y mm | Profiled | Ensure minimal deflection for uniform roundness |
Cable Stranding Process
The Cable Stranding Process is an integral part of cable and rope manufacturing, combining multiple wires into a single conductor. It’s essential for enhancing the flexibility and strength of the cable. Let’s take a closer look at this process.
Stranding Machine Setup
When setting up stranding machines, your objective is to arrange the components to prepare for the winding of wires around a common axis. You’ll encounter different machine types, each suited for specific stranding methods:
- Bow Cablers: Excellent for assembling bare and insulated conductors, ensuring high productivity.
- Roll Form Stranders: Known for their speed and ability to produce compact strands while offering cost savings.
Typically, these machines involve multiple pay-offs that rotate around the axis, providing a continuous feed of wire at a controlled speed.
Forming Stranded Conductors
Forming stranded conductors is a delicate balance between precision and efficiency. Here’s what you should know:
- Conductor Types:
- Milliken conductors: For reducing AC losses in high-current applications.
- Sector conductors: Shaped conductors to maximize packing density.
- Stranding Methods:
- Stranded conductors are formed by winding individual wires, achieving greater flexibility and mitigating the risk of wire fatigue.
Remember, the key to high-quality cabling lies in the precise rotating movements and maintaining an optimal speed during the stranding process. This ensures that individual wires are uniformly wound to form a robust conductor.
Wire Drawing and Annealing
In the cable round roller production process, your first step is to use draw dies to shape the wire. This method, called wire drawing, involves pulling the wire through a series of increasingly smaller dies to reduce its diameter. This action requires considerable tension to be effectively done.
During the drawing process, the metal rod is fed into an initial die, which begins the transformation into a thinner wire. Each subsequent die decreases the wire’s size further. Rollers are often utilized to guide and maintain the wire’s tension, ensuring the dimensional consistency necessary for quality.
However, drawing increases the wire’s strength while reducing its flexibility. To regain flexibility and decrease internal stresses from the drawing process, you anneal the wire. Annealing involves heating the wire to a specific temperature and then slowly cooling it. This heat treatment makes the wire more malleable and returns some of its ductility, essential for further processing.
Insulation and Extrusion Process
When producing cable, the insulation and extrusion process are essential for ensuring cable reliability and functionality. Your understanding of this will be crucial for grasping the overall cable round roller production process.
Extrusion Techniques
Extrusion is the heart of cable insulation.
- Pressure Extrusion: This technique involves exerting pressure to fill voids within the cable structure.
Materials are heated and pushed through a die to create the insulation layer around the conductive core. The process demands precise control over temperature and pressure to maintain insulation consistency.
- Cooling: Post-extrusion, cooling happens to solidify the cable insulation. This is typically done via a cooling trough or water bath.
In cable extrusion, maintaining a consistent section throughout the length is crucial. Specialized equipment, like crossheads, guide and shape the cable during this process.
Applying the Outer Sheath
After insulating the core, applying the outer sheath is your next step.
- Tunnels: To apply the outer sheath, the cable passes through a long tunnel where the sheathing material is applied.
- Material Options: The materials used for the outer sheath vary, with choices like PVC, polyethylene, or rubber, depending on the cable’s intended use.
The process involves another layer of extrusion, wherein the sheathing material is applied over the insulated core to protect against environmental factors and mechanical stresses. The outer sheath contributes significantly to the cable’s overall durability and reliability.
Product Testing and Quality Control
Your cable round roller has to go through stringent product testing and quality control to ensure reliability and consistent performance in diverse conditions.
Electrical Testing
Electrical testing of your cable round roller ensures that the product is safe and meets electromagnetic compatibility requirements. This process requires the roller to undergo:
- Conductivity Tests: To verify the efficient transmission of electrical current.
- Dielectric Tests: To check the insulation’s ability to withstand electrical stress.
- High Voltage Tests: These are critical to confirm that the roller maintains its properties under extreme voltage conditions and is flexible enough to handle the varying electrical loads it will encounter.
Mechanical Testing
Mechanical testing assesses the mechanical properties and robustness of your cable round roller. Tests include:
- Tensile Strength Test: To determine the stress and strain tolerance before failure.
- Flexibility Test: Here you learn how your roller behaves under repeated bending or flexing, a crucial indicator of its flexibility and life cycle.
- Impact Resistance: This identifies the roller’s ability to withstand sudden and forceful impacts, guaranteeing that it will continue to function under rough handling or environmental stress.
Cable Drum Winding and Packaging
When producing cable round rollers, the focus on cable drum winding and packaging is paramount for ensuring the product’s integrity and ease of use for your clients.
During the winding process, your cable is precisely coiled onto a take-up drum. This drum is specifically chosen for its compatibility with the weight and length of your intended cable roll. It is vital to avoid exceeding the minimum safe bending radius to prevent damage to the cable.
For successful winding, follow these steps:
- Set up your drum twister, which is responsible for the controlled rotation and cable lay.
- Secure the cable’s end to the take-up drum.
- Begin winding, ensuring the tension is consistent to avoid any loose or overly tight coils.
As for packaging, bobbins are utilized to keep the cable ends neat and prevent unraveling during transportation. The bobbins also facilitate the unwinding process from the drum.
Packaging tips:
- Ensure drums are robust enough to handle the cable’s weight.
- Use protective wrapping to safeguard the cable from environmental hazards.
- Place bobbins at both ends of the cable on the drum to secure loose ends.
Environmental and Energy Considerations
When you’re involved in the production of cable round rollers, it’s essential to consider both the environmental and energy impacts of the process. The manufacture of these rollers can consume significant amounts of energy, which in turn has implications for greenhouse gas emissions and climate change.
Energy Source
The source of electrical energy used during the production plays a crucial role. Regenerative energies, such as solar or wind power, substantially reduce the environmental footprint as opposed to relying on fossil fuels or the shut-down of nuclear power plants.
Energy Efficiency
Manufacturing processes should aim to be as energy efficient as possible. Optimal energy consumption is achieved through:
- Streamlining the production line
- Ensuring machinery operates at peak efficiency
- Regular maintenance to prevent energy wastage
Recycling and Waste Reduction
Emphasize recycling and efficient waste management. Using recycled materials when possible reduces the demand for virgin resources and minimizes waste.
Process Improvements
Innovative process improvements can lead to:
- Reduction in energy required for baling
- Enhanced roller quality, which affects durability and longevity
- Less frequent replacement and lower environmental impact
By taking into account these aspects, you contribute to a more sustainable approach in the cable round roller production process.